Textile designer: Margo Selby
Colourful, three-dimensional fabrics lie at the heart of this designer-weaver’s vibrant cushions, throws, rugs and home accessories
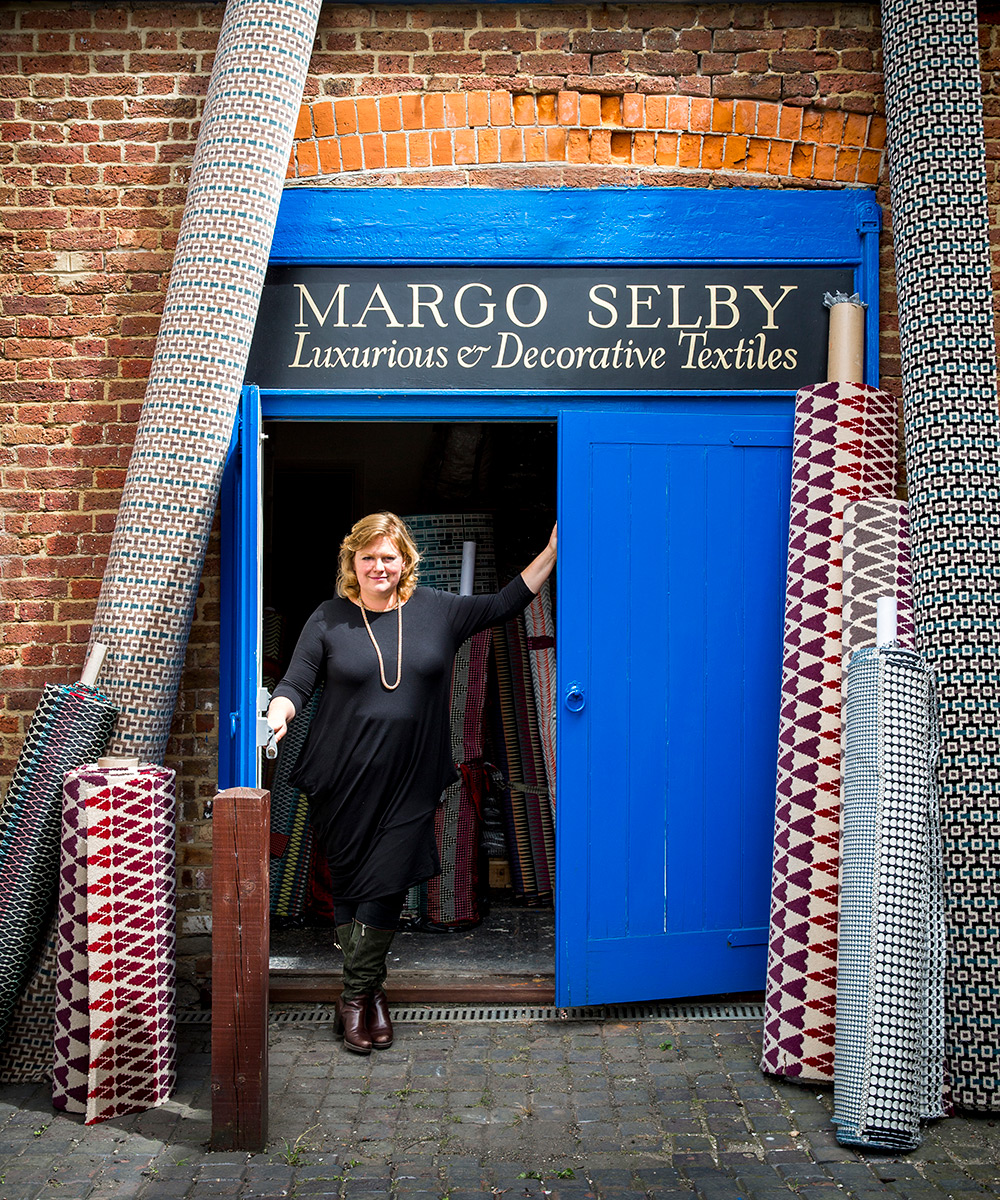
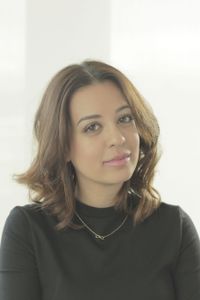
Uniting ancient weaving techniques with industrial mill production, Margo Selby has been creating innovative hand-woven textiles for more than a decade. The weaver’s trademark three-dimensional fabrics, known for their strong graphics and pattern, are created at her Kent studio on a 24-shaft dobby loom, before being produced by specialist mills.
Margo’s ranges encompass furniture, lighting and home accessories, and she has also recently collaborated on a carpet collection with Alternative Flooring.
See: Textile trends – the latest looks for fabrics
There is a history in my family of women making textiles in the home. My grandmother, Edith Selby, known as Janie, taught me to crotchet and cross-stitch, so it was an obvious choice to concentrate on textiles when I did my foundation at Chelsea College of Arts. I enjoyed many different medias during my studies, though, especially graphic work, sculpture and three-dimensional design.
I studied for an MA in woven textiles at the Royal College of Art and was then awarded a fellowship at The Ann Sutton Foundation. Some of the projects we worked on there included developing products for Shetland wool and designing dobby fabrics to be woven in Yorkshire for the interiors fabric industry. It was here that I formed my first connections with mills. I started to combine my hand-woven ideas with industrial processes and the result was the silk and Lycra fabrics that were to become the trademark of my brand.
The concept of three-dimensional fabric came about because I was always drawn to surface and texture.I thought it would be interesting to try to recreate the feel of bubble wrap packaging in silk. I researched different fibres that would shrink when heated and tried weaving them in combination with silk to create three-dimensional surfaces.
My inspiration comes from weaving. It is the starting point for all my designs, so as well as the work I develop on my own handloom, I enjoy researching what is happening in woven textiles around the world. I am stimulated by highly decorative design that incorporates lots of pattern and colour. Our most recent collections reference indigenous and tribal fabrics, including Japanese dyeing and African prints.
Design expertise in your inbox – from inspiring decorating ideas and beautiful celebrity homes to practical gardening advice and shopping round-ups.
When I create a fabric, I start by designing the warp. It goes on to the loom with tension and forms a series of taut threads similar to a string instrument. Into this we weave the weft yarns, which can be changeable. The warp is the backbone of the fabric and an integral part of the design, and it cannot be changed once the fabric is on the loom. In the warp, I experiment with weaving different structures and weft yarns until I have a product I am happy with. The weaving is slow and methodical and the fabric grows, one row or pick at a time, giving much contemplation time for design. Once I am happy with a fabric, often after many warps developing the idea, I then explore the possibility for production with an industrial mill. In the case of my flooring collection, we have translated the woven patterns into a carpet construction, which is made in the UK.
We all work in an open-plan studio in Whitstable. The office and the looms are together so I can hear what’s happening in the business while I am weaving. I try to surround myself with material, yarn and images that inspire me as well as designs in progress. I spend the first two hours of the day dealing with emails and working with the team on various projects before sitting at my loom for the rest of the day.
I previously collaborated with Alternative Flooring to create my first wool carpet and runner designs. They are inspired by a collection of deflected double-weave hand-woven cloths that I have been developing on my handloom in the studio over the past few years.
I buy yarn from anywhere I can find it. Japan and the US are particularly good for hand-woven varieties, as they have a vibrant hand-weaving community. We try to find the very best weavers for the type of material we are working with.
I started the business in my bedroom. Since then, it has grown to include a busy textile studio employing eight full-time members of staff and a team of piece workers in Whitstable, weaving bespoke textiles for a wide variety of end uses. The handloom and the craft of weaving remains central to all our products. Working on flooring for the first time and witnessing both carpet and colour come back into fashion is an exciting development, too. Seeing my designs, originally produced as soft silk and wool fabrics, blown up and recoloured to make them suitable for flooring is very satisfying. We are also focusing on developing interiors fabrics to be sold by the metre, as well as diversifying our accessories range into bedlinen and towels.
Margo Selby, 01227 282758, margoselby.com.
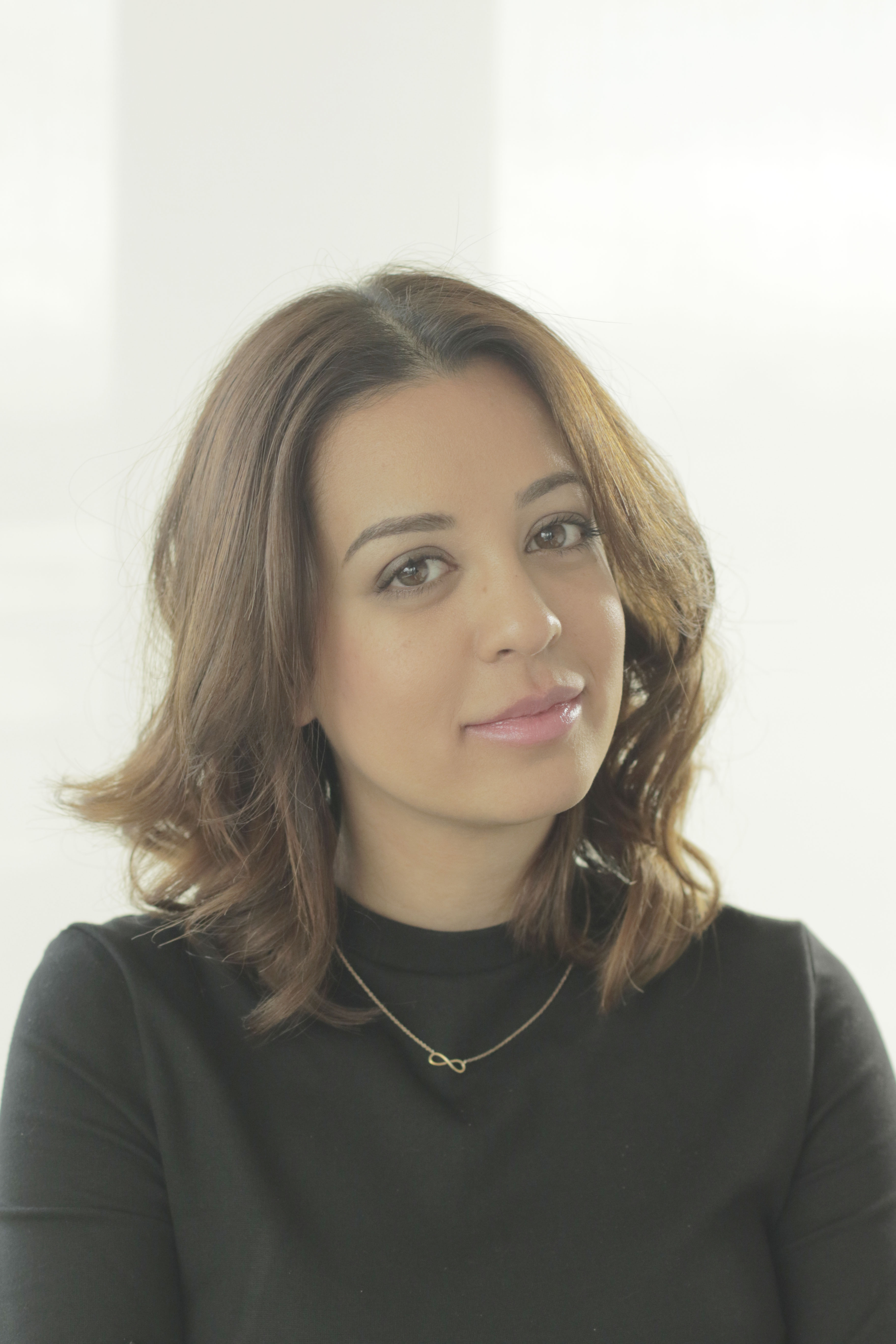
Jennifer is the Digital Editor at Homes & Gardens, bringing years of interiors experience across the US and UK. She has worked with leading publications, blending expertise in PR, marketing, social media, commercial strategy, and e-commerce. Jennifer has covered every corner of the home – curating projects from top interior designers, sourcing celebrity properties, reviewing appliances, and delivering timely news. Now, she channels her digital skills into shaping the world’s leading interiors website.